在鋁合金壓力加工過程中, 一般是由原鋁錠重熔、配制合金、鑄造成鑄錠, 再經(jīng)軋制、擠壓、鍛造等生產(chǎn)成鋁材在原鋁錠第一次投人到生產(chǎn)中產(chǎn)生的廢料循環(huán)使用, 直至完全變成成品的過程中, 有一部分鋁錠由于氧化、燒損而消耗掉了, 此損耗量與鋁錠投人量之比稱之為原鋁錠損耗率本文對(duì)此進(jìn)行研究, 并推導(dǎo)出鋁錠損耗率的一般計(jì)算公式。
1.原銘錠損耗率的影響因素
影響鋁錠損耗率的主要因素有原鋁錠一次投料燒損, 廢料再次投人燒損及綜合成品率
1.1一次投料燒損率
一次投料燒損率主要受合金種類、爐型、爐內(nèi)氣氛、熔煉(詞條“熔煉”由行業(yè)大百科提供)溫度及時(shí)間等因素的影響較大如合金中含鎂、鏗則易氧化燒損熔煉爐(詞條“熔煉爐”由行業(yè)大百科提供)熔池的形狀及加熱方式對(duì)燒損都有影響, 采用火焰爐的燒損率較大, 一般為1.5%~3.5%采用電阻反射爐的燒爐率為1.0%~1.5%采用低頻感應(yīng)爐的燒損率為0.4%~0.6在比較落后的熔煉工廠中, 一般采用火焰爐熔化原鋁錠、粗調(diào)化學(xué)成分, 在電爐內(nèi)精調(diào)化學(xué)成分, 在靜置爐內(nèi)除氣, 總燒損率為熔體隨著熔煉溫度升高、保溫時(shí)間加長(zhǎng), 氧化燒損加大
1.2反復(fù)投料燒損率
反復(fù)投料燒損率是指由熔鑄至成品的過程中,各工序產(chǎn)生的廢料在回爐熔化進(jìn)一步加工至成品的一次加工過程中, 損耗掉的廢料量占廢料投人量的百分比它除了受一次投料燒損的影響因素制約外, 還主要受廢料的表面狀態(tài)影響一級(jí)廢料, 即大塊廢料燒損率為3.0%~4.5%二級(jí)廢料, 即打捆薄片廢料、薄壁型材頭尾等的燒損率為3.0%~10%三級(jí)廢料, 即碎屑的燒損率可達(dá)13%~30%對(duì)于某一合金品種而言, 廢品結(jié)構(gòu)基本一定, 反復(fù)投料燒損率在一個(gè)很小的范圍內(nèi)波動(dòng)反復(fù)投料燒損率可通過下面公式計(jì)算:

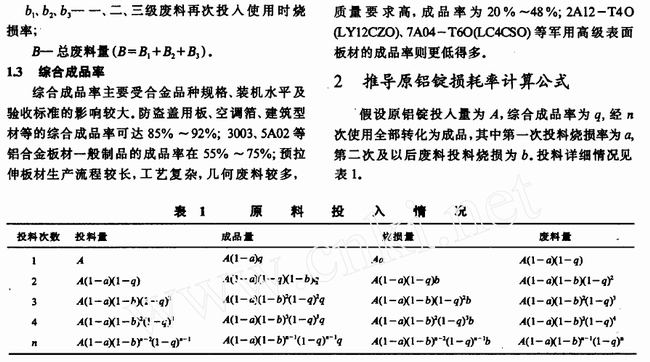
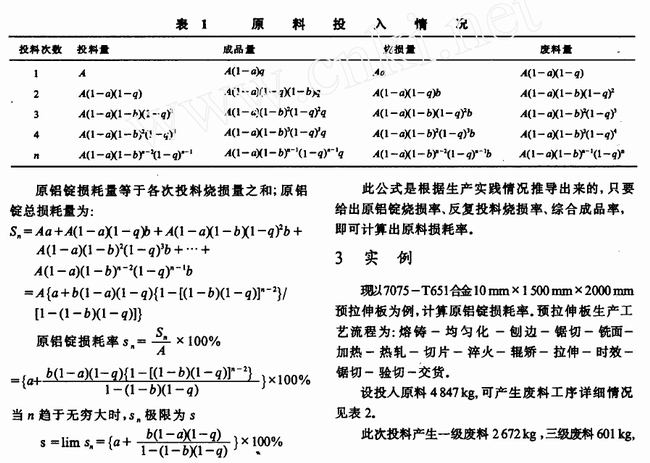
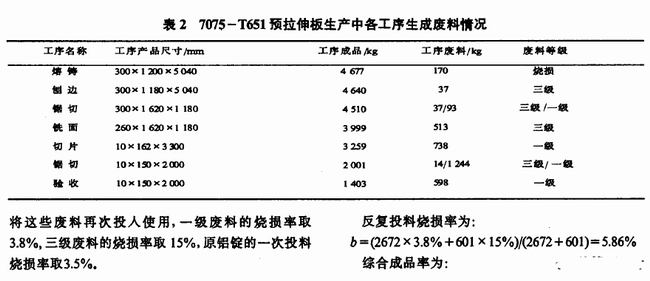
擊下發(fā)生激烈的塑性變形, 伴隨著塑性變形過程晶體發(fā)生滑移, 導(dǎo)致亞晶粒內(nèi)位錯(cuò)密度的增加, 晶格畸變, 晶格間距發(fā)生變化噴砂后在表層將獲得較為細(xì)密的顯微組織。
在噴砂過程中,表層金屬經(jīng)歷了易滑移階段和形變強(qiáng)化等階段在易滑移階段,對(duì)變形提供主要貢獻(xiàn)的是出現(xiàn)在晶體表面的位錯(cuò)。在低于結(jié)晶溫度下, 位錯(cuò)對(duì)潛在的變形能有重要影響在塑性滑移條件下單位體積內(nèi)的機(jī)械變形功將等于系統(tǒng)在單位體積中形成單位位錯(cuò)時(shí)熱力勢(shì)的增加現(xiàn)代形變強(qiáng)化理論認(rèn)為位錯(cuò)形成了平面(詞條“平面”由行業(yè)大百科提供)塞積群,它由幾個(gè)受滑移面障礙阻滯的平面位錯(cuò)組成,其結(jié)果是流變應(yīng)力增大塞積群位錯(cuò)的交互作用導(dǎo)致每一個(gè)位錯(cuò)能加。這樣將使表面位錯(cuò)的化學(xué)位能增加這種表面化學(xué)位和表面活化能的改變對(duì)其后的陽(yáng)極氧化的影響主要體現(xiàn)在導(dǎo)致陽(yáng)極氧化時(shí)兩極過電位和陽(yáng)極表面活化能的改變?cè)陉?yáng)極氧化的阻擋層生成過程中,氧化電流服從下述公式

從上述公式可以看出表層組織的改變將會(huì)通過影響氧化電流而直接影響氧化膜(詞條“氧化膜”由行業(yè)大百科提供)層的性能隨著表面活化能和兩極過電位的增加, 其氧化電流減少, 結(jié)果在同樣的氧化時(shí)間內(nèi)獲得的氧化膜致密層減薄, 耐蝕性降低。
結(jié)束語(yǔ)
在不同預(yù)處理條件下, 由于砂面形成機(jī)理的不同,鋁型材表面微觀形貌、表層晶體組織結(jié)構(gòu)、表面活化能也有本質(zhì)的區(qū)別這些將直接或間接地對(duì)陽(yáng)極氧化膜層性能有著重要的影響。在生產(chǎn)實(shí)踐中如果不加區(qū)別地將堿蝕洗工藝流程中的工藝參數(shù)照搬到噴砂工藝流程中來(lái),可能使產(chǎn)品不合格要想獲得合格的產(chǎn)品, 必須確立合理的表面預(yù)處理路線和最佳工藝參數(shù), 如噴砂工藝中磨粒性質(zhì)如粒度、材質(zhì)、硬度和工藝參數(shù)如噴射壓力、壓縮空氣量、噴射時(shí)間、表面覆蓋率砂面后堿洗和中和工藝參數(shù)的合理調(diào)整在陽(yáng)極氧化工藝中, 應(yīng)考慮預(yù)處理對(duì)型材表面狀態(tài)的影響, 可以通過合理的實(shí)驗(yàn)設(shè)計(jì), 充分運(yùn)用現(xiàn)代優(yōu)化實(shí)驗(yàn)設(shè)計(jì)技術(shù)尋求最佳工藝參數(shù)。